Unveiling the Transformative Power of Data in Welding: A Journey with K-TIG
In the dynamic landscape of modern manufacturing, the integration of data-driven technologies has ushered in a new era of efficiency, precision, and productivity. Within the realm of welding, where precision and quality are paramount, the utilization of data captured from welding controllers has emerged as a cornerstone of Industry 4.0, revolutionizing traditional workflows and unleashing a myriad of benefits across diverse industries.
Enhanced Process Control and Optimization
Data captured from welding controllers serves as a treasure trove of insights, offering real-time visibility into critical parameters such as arc voltage, current profiles, weld speed, and heat input. By leveraging this wealth of information, manufacturers can fine-tune their welding processes, optimize parameters, and achieve unprecedented levels of precision and consistency. For instance, in automotive manufacturing, the ability to precisely control welding parameters ensures uniformity in welds, leading to enhanced structural integrity and performance across vehicle assemblies.
Predictive Maintenance and Fault Detection
One of the transformative capabilities unlocked by data-driven welding controllers is the ability to anticipate and mitigate potential issues through predictive maintenance and fault detection algorithms. By analyzing historical data trends and performance metrics, manufacturers can identify early warning signs of equipment degradation, component wear, or process anomalies, enabling proactive maintenance interventions and minimizing costly downtime. In heavy machinery fabrication, for instance, predictive maintenance based on data insights helps prevent equipment failures, optimize uptime, and ensure seamless production continuity.
Quality Assurance and Compliance
In industries where adherence to stringent quality standards is non-negotiable, data captured from welding controllers serves as a linchpin of quality assurance and compliance. By monitoring key welding parameters in real time and recording process data for traceability, manufacturers can validate weld quality, detect deviations from specifications, and document compliance with regulatory requirements. In aerospace manufacturing, for example, the meticulous analysis of welding data ensures compliance with stringent industry standards, safeguarding the integrity and safety of aircraft structures while facilitating regulatory audits and certifications.
Optimized Resource Allocation and Inventory Management
Data-driven insights derived from welding controllers empower manufacturers to optimize resource allocation, streamline inventory management, and enhance operational efficiency. By correlating welding data with production schedules, material consumption rates, and inventory levels, manufacturers can optimize weld sequencing, minimize material waste, and synchronize supply chain activities for just-in-time replenishment. In shipbuilding, for instance, data-driven inventory management ensures seamless coordination of welding operations across vast shipyards, optimizing resource utilization and minimizing excess inventory holding costs.
Empowering Human-Machine Collaboration
In the era of Industry 4.0, the convergence of data-driven technologies and human expertise fosters a paradigm of collaborative manufacturing, where humans and machines synergize to achieve unparalleled levels of productivity and innovation. By providing welders with real-time feedback, actionable insights, and augmented decision support tools, data captured from welding controllers enhances human-machine collaboration, empowers workers with digital skills, and fosters a culture of continuous improvement. In metal fabrication workshops, for example, welders equipped with advanced controllers with data visualization capabilities leverage real-time welding data to optimize technique, improve weld quality, and drive operational excellence.
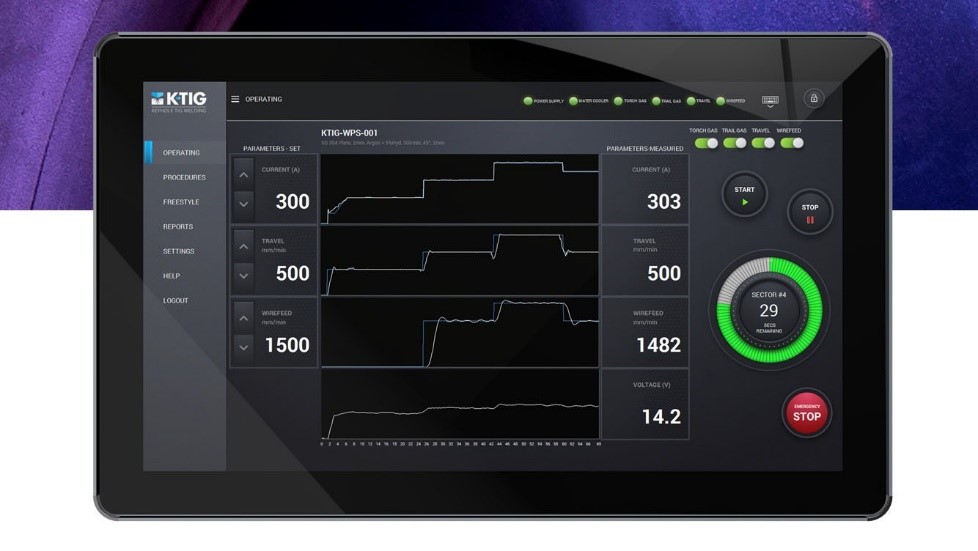
K-TIG provides the pathway to Industry 4.0
Transitioning from the theoretical discussion of data-driven welding to real-world applications, K-TIG welding technology emerges as a tangible pathway toward achieving the lofty ideals of Industry 4.0. At the heart of this transformative approach lies the K-TIG controller, a cutting-edge tool that bridges the gap between traditional welding practices and the digital era, empowering manufacturers to harness the full potential of data-driven insights while reaping the benefits of increased productivity, efficiency, and quality.
Seamless Integration of K-TIG Technology into Industry 4.0 Frameworks
In the context of Industry 4.0, where interconnected cyber-physical systems drive automation, optimization, and innovation, K-TIG welding technology serves as a cornerstone of digital transformation. By seamlessly integrating with existing manufacturing ecosystems, the K-TIG controller facilitates the seamless exchange of data between welding processes, production systems, and enterprise-wide information networks, laying the foundation for interconnected, data-driven workflows that transcend traditional boundaries.
Advanced Capabilities for Real-Time Monitoring and Control
The K-TIG controller boasts advanced capabilities for real-time monitoring, control, and analysis of welding parameters, offering unprecedented levels of visibility and insight into the welding process. From arc stability, travel speed, heat inputs, wire feed rate, and automation control the K-TIG controller captures granular data with precision and accuracy, enabling welders to make informed decisions, optimize parameters, and ensure consistent, high-quality results.
Predictive Analytics for Proactive Maintenance and Performance Optimization
Building upon the foundation of data-driven insights, the K-TIG controller empowers manufacturers to deploy predictive analytics algorithms for proactive maintenance and performance optimization. By leveraging historical data trends, machine learning algorithms, and predictive modeling techniques, the K-TIG controller anticipates potential equipment failures, identifies optimization opportunities, and recommends actionable strategies for maximizing uptime, minimizing downtime, and enhancing overall equipment effectiveness.
Enhanced Collaboration and Knowledge Sharing
In the collaborative ecosystem of Industry 4.0, the K-TIG controller serves as a catalyst for enhanced collaboration and knowledge sharing across multidisciplinary teams. Through intuitive user interfaces, interactive dashboards, and analytics platforms, the K-TIG controller facilitates seamless communication, collaboration, and knowledge exchange among welders, engineers, data scientists, and domain experts, fostering a culture of continuous learning, innovation, and improvement.
Pathways to Sustainable Growth and Competitive Advantage
By embracing K-TIG welding technology and the transformative capabilities of the K-TIG controller, manufacturers unlock pathways to sustainable growth, competitive advantage, and market differentiation in the digital age. From streamlined production workflows and optimized resource allocation to enhanced product quality and customer satisfaction, the adoption of K-TIG technology enables manufacturers to stay agile, responsive, and resilient in the face of evolving market dynamics, technological disruptions, and competitive pressures.
In essence, the transition from discussion topic to reality is exemplified by the tangible impact of K-TIG welding technology and the transformative capabilities of the K-TIG controller in reshaping the landscape of modern manufacturing. As we embark on this journey towards Industry 4.0 excellence, fueled by innovation, collaboration, and data-driven insights, let us embrace the transformative potential of K-TIG technology, unlock new horizons of productivity and efficiency, and propel our industries towards a future defined by excellence, sustainability, and prosperity.
We are here to help
If you're a welding company looking to improve your productivity, efficiency, and competitiveness, it's time to consider the benefits of welding automation and the K-TIG welding system. By automating your welding processes, you can reduce welding time and labor costs, while also improving weld quality and consistency.
The K-TIG system is a powerful and cost-effective solution for automating your welding processes. Its advanced technology allows for high-quality welds to be produced quickly and efficiently, making it a valuable investment for any welding operation.
So if you want to take your welding business to the next level, it's time to take action. Contact a K-TIG representative today to learn more about how their welding automation solutions can help your business achieve its goals. Don't let the global welder shortage or the increasing competition hold you back - invest in welding automation and the K-TIG system today to stay ahead of the curve.